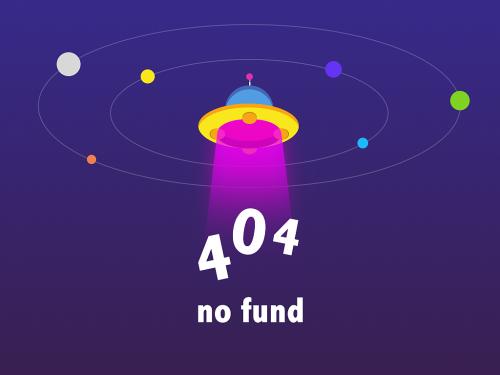
about aluminium
aluminium is mostly used in form of alloys of pure aluminium in combination with other elements in order to improve the mechanical properties of the metal, especially to increase strength and corrosion resistance of the metal.
combining different elements to contribute to different properties of the finished products:
fe → increasing the strength
si → in combination with mg for higher strength
cu → increasing the mechanical properties, reduces corrosion-resistance
mn → increasing the mechanical properties, changing the deep-drawing quality
mg → high strength after cold forming
cr → more strength in combination with elements like cu, mn, mg
ti → higher strength
zn → reduces corrosion-resistance
main aluminium-alloy family groups
series |
alloys with their main elements |
typical applications |
1xxx |
99.00% min aluminium |
foil, litho-sheet, sheet |
2xxx |
aluminium-copper |
aircraft industry |
3xxx |
aluminium-manganese |
cans, building radiators |
4xxx |
aluminium-silicon |
heat exchangers & engineering |
5xxx |
aluminium-magnesium |
cans, automobile, facades, building, transportation |
6xxx |
aluminium-magnesium und silicon |
automobile, building, transportation |
7xxx |
aluminium-zinc |
aircraft industry, radiators |
8xxx |
other elements |
foil (fe), aircraft industry (li) |
aluminum alloy for coil coating
general speaking, the aluminum alloys used in coil coating are from the 1***, 3*** and 5*** alloys. the choice of alloy, gauge and temper will depend on the specific application, optimizing for the balance between strength and formability required by the product.
for example:
aa3005 h48 is used for roller shutters. where, 3005 refers to an alloy with 0.5% manganese and 0.5% magnesium, while the h48 designation refers to a cold rolled (h) painted (4) product with 75% residual hardening (6). this would typically be used in a thickness of
aa5754 h42 used for facades. here, 5754 refers to an allow with 3% magnesium, while the h42 designation refers to a cold rolled (h) painted (4) product with 15% residual hardening (6).
alloys fall into two main groups. the strain-hardening alloys, where strength is achieved by the amount of "cold work" applied to the alloy and heat-treatable or precipitation hardening alloys, where the strength and properties are achieved by heat treatments of varying complexity.
the temper designations and definitions are as follows:
· f as fabricated
· o annealed
· h strain hardened
· w solution heat treated
· t thermally treated to produce stable tempers other than f, o or h.
considering the strain hardened h temper, the first number indicates a specific operation. specifically,
· h1x strain hardened only
· h2x strain hardened and partially annealed
· h3x strain hardened and stabilized
· h4x strain hardened plus lacquering or painting.
thus in coil coating the h4x temper prevails.
the final digit indicates the ultimate tensile strength:
· hx2 has 15% residual hardening
· hx4 has 35% residual hardening
· hx6 has 55% residual hardening
· hx8 has 75% residual hardening